Easy Implementation of ERPNext for Distribution Businesses
ERPNext is a software solution designed to help small and medium-sized businesses manage their operations more efficiently.
In today's fast-paced & rapidly evolving business environment, distribution businesses are looking for ways to streamline their operations & increase efficiency. Enterprise Resource Planning (ERP) systems have been a game-changer for many businesses in this regard. It helps in streamlining business operations by integrating 7 automating various functions. In this article, we will discuss the benefits of implementing ERPNext for distribution businesses & how to implement it for smooth operations easily.
What is ERPNext?
ERPNext is a software solution developed for small & medium-sized distribution businesses. It helps to integrate all the essential functions of a distribution business such as supply chain management, order management, inventory management, warehouse management, financial management, & customer relationship management. With ERPNext, businesses can get real-time insights into various aspects of their operations, which can help to reduce errors, optimize processes, & improve customer satisfaction. In short, ERPNext is a useful tool that helps businesses run more efficiently.
What are ERP Implementation Phases?
ERP implementation is a multi-step process that includes the following phases:
Step-1: Planning:
In this phase, the business determines its goals & objectives for implementing the ERP system. It involves defining the scope of the project, establishing timelines, & identifying the resources needed for the project.
Step-2: Design:
The design phase involves configuring the ERP software to meet the specific requirements of the business. This may involve customizing the software to match the business processes, creating workflows, defining roles & responsibilities, & setting up data structures.
Step-3: Configuration:
Once the design phase is complete, the ERP system is configured to meet the requirements of the business. This includes setting up the software, installing hardware & software components, & integrating the system with other applications.
Step-4: Testing:
In this phase, the ERP system is tested to confirm all the business requirements are perfect. This includes performing various tests such as system integration testing, user acceptance testing, & performance testing.
Step-5: Deployment:
Once the ERP system is tested & approved, it is deployed to the live environment. This involves migrating data from legacy systems, training users, & ensuring that the system is ready to go live.
Step-6: Maintenance:
The maintenance phase involves ongoing support & maintenance of the ERP system. This includes monitoring system performance, troubleshooting issues, providing user support, & making upgrades & enhancements as required.
Benefits of ERPNext in the Distribution industry:
The distribution industry is a complicated & competitive sector that requires constant attention to various aspects of the supply chain to make sure that products are delivered to customers on time & in good condition. To help with this, many distribution companies have started using Enterprise Resource Planning (ERP) software solutions such as ERPNext. Here are some benefits of implementing ERPNext in the distribution industry:
1. Improved Visibility:
ERPNext provides real-time visibility into different aspects of the distribution business, including sales orders, inventory levels, & warehouse management. This helps businesses to make informed decisions quickly & to optimize their processes for better efficiency.
2. Reduced Errors:
Manual data entry is prone to errors, which can lead to wrong information being recorded & delays in order processing. With ERPNext, businesses can automate their processes, reducing the chances of errors & improving the accuracy of information.
3. Enhanced Customer Satisfaction:
With the help of ERPNext, businesses can make sure that products are delivered to customers on time & in good condition. This can lead to enhance customer satisfaction, which is necessary for the success of any business.
4. Increased Efficiency:
ERPNext helps businesses to automate their processes, reducing the need for manual data entry & streamlining workflows. This can lead to increased efficiency, reduced operational costs, & improved profitability.
5. Better Financial Management:
ERPNext delivers businesses with a comprehensive financial management solution that includes accounting, budgeting, & cash flow management. This helps businesses to track their finances more accurately based on their financial data.
6. Cloud-Based Solution:
ERPNext is a cloud-based solution, which means that it can be accessed from anywhere with an internet connection. This makes it simple for businesses to manage their operations remotely & to collaborate with team members in various locations.
How ERPNext Can Be Easily Implemented For Smooth Operations?
ERPNext can be easily implemented for smooth operations by following a structured approach that takes into consideration the unique requirements of each business. Here are some key points to keep in mind:
1. Define your business processes:
Before implementing ERPNext, it's important to determine your business processes in detail. This includes everything from sales & purchasing to inventory management & customer support. Once you have a clear understanding of your processes, you can better configure ERPNext to meet your specific requirements.
2. Configure ERPNext to meet your needs:
ERPNext is highly customizable & can be configured to meet the specific needs of your business. This includes setting up modules, customizing workflows, & creating reports. ERPNext also has a powerful API that can be used to integrate with other systems or develop custom applications.
3. Train your staff:
To make sure a smooth implementation, it's essential to train your staff on how to use ERPNext. This includes training on basic navigation, data entry, & report generation. Additionally, you may need to provide specialized training for certain modules or workflows.
4. Test and refine:
Once you have configured ERPNext & trained your staff, it's important to test the system thoroughly. This includes running tests on all modules & workflows, as well as conducting user acceptance testing. Based on the results of testing, you may need to refine certain aspects of the system to make sure optimal performance.
5. Continuous improvement:
ERPNext is a robust tool that can help to optimize your business processes & increase efficiency. However, it's important to remember that continuous improvement is essential to confirm that the system is meeting your changing business needs. This may include adding new modules, workflows, or custom applications and updating existing processes to better align with your business goals.
Five Signs You Need a Distribution ERP:
Implementing an ERP system for distribution businesses can help to solve several challenges that are faced in managing the operations of the business. Here are five signs that indicate the need for a distribution ERP system:
1. Your customers aren't happy:
If your customers complain about late or wrong deliveries, it could be a sign that your current distribution management system could be more efficient. An ERP system can optimize your order management & fulfillment processes, ensuring that customers receive their orders on time & accurately.
2. Your processes are clunky:
If you find that your business processes are slow, manual, & time-consuming, it's likely that you need an ERP system. An ERP system can automate many of the repetitive tasks involved in distribution, freeing up staff time for more strategic activities.
3. Your data is all over the place:
If you find that you have to access multiple systems or spreadsheets to get a complete view of your business data, it's time to consider an ERP system. An ERP system can integrate all your business data into a single source, providing real-time insights into your operations.
4. You can't grow:
If you're finding it difficult to scale up your operations due to manual processes & lack of visibility, an ERP system can help. With an ERP system, you can automate many of your operations, reducing the need for manual intervention, & providing real-time insights into your business performance.
5. You can't keep up with demand:
If you're struggling to fulfill customer demand due to inefficient processes, an ERP system can help. An ERP system can optimize your warehouse & inventory management processes, ensuring that you have the right inventory levels to fulfill customer orders on time.
ERP Best Practices for Manufacturing & Distribution Companies
In the manufacturing & distribution industries, ERP systems are particularly important as they help to optimize operations, streamline processes, & enhance supply chain management. Here are some best practices for manufacturing and distribution companies looking to implement an ERP system:
1. Understand your business needs:
Before implementing an ERP system, it is essential to understand your business needs & the specific areas that need improvement. Conducting a thorough analysis of your current business processes, and identifying bottlenecks & pain points can help you to determine the specific functions that you need from an ERP system.
2. Choose the right software:
Once you have identified your business needs, you can start researching & selecting the appropriate ERP software that meets those needs. Factors to consider when selecting an ERP system include features, scalability, customization options, support, & cost.
3. Involve stakeholders:
The success of ERP implementation depends on the involvement of all stakeholders, including top management, employees, & customers. You have to involve all stakeholders from the beginning to make sure buy-in, support, & collaboration throughout the implementation process.
4. Plan for change management:
ERP implementation often requires changes in processes & workflows. It is essential to plan for change management to make sure of a smooth transition to the new system. This involves training employees, communicating changes, & identifying champions who can drive adoption.
5. Focus on data accuracy:
Data accuracy is essential for the success of an ERP system. Ensure that data is accurate, complete, & up-to-date to ensure that the system can deliver accurate insights and reports.
6. Customize to your needs:
While most ERP systems are developed to meet the needs of a wide range of businesses, it is essential to customize the system to your specific needs. Customization helps to enhance the system's efficiency, usability, & effectiveness.
7. Monitor and optimize:
Once the ERP system is up & running, you need to monitor its performance & optimize it for maximum efficiency. This involves identifying & addressing issues, continuously improving processes, & ensuring that the system is up-to-date with the latest technologies.
Conclusion-
With the implementation of ERPNext, distribution businesses can run more efficiently, save costs, & enhance their overall performance. By following the best practices outlined in this article, businesses can make sure of a smooth & simple implementation of ERPNext, & reap the advantages of this powerful software solution.
To learn more about ERPNext, be sure to check out - Hybrowlabs ERPNext Development Services & Hybrowlabs Manufacturing ERPNext Services.
FAQ-
1. What are the signs that a distribution business needs an ERP system?
Some signs that a distribution business needs an ERP system include unhappy customers, clunky processes, scattered data, inability to grow, and inability to keep up with demand.
2. What are some ERP best practices for distribution companies?
ERP best practices for manufacturing and distribution companies include understanding business needs, choosing the right software, involving stakeholders, planning for change management, focusing on data accuracy, customizing the system, and monitoring and optimizing the system's performance.
3. How does ERPNext help with supply chain management?
ERPNext helps with supply chain management by providing real-time visibility into inventory levels, tracking orders, managing suppliers, and streamlining logistics.
4. Can ERPNext be customized for specific business needs?
Yes, ERPNext can be customized to meet specific business needs. Customization helps to enhance the system's efficiency, usability, and effectiveness.
5. Is ERPNext suitable for small and medium-sized businesses?
Yes, ERPNext is specifically designed for small and medium-sized distribution businesses. It provides affordable and scalable solutions for businesses that want to streamline their operations and increase efficiency.
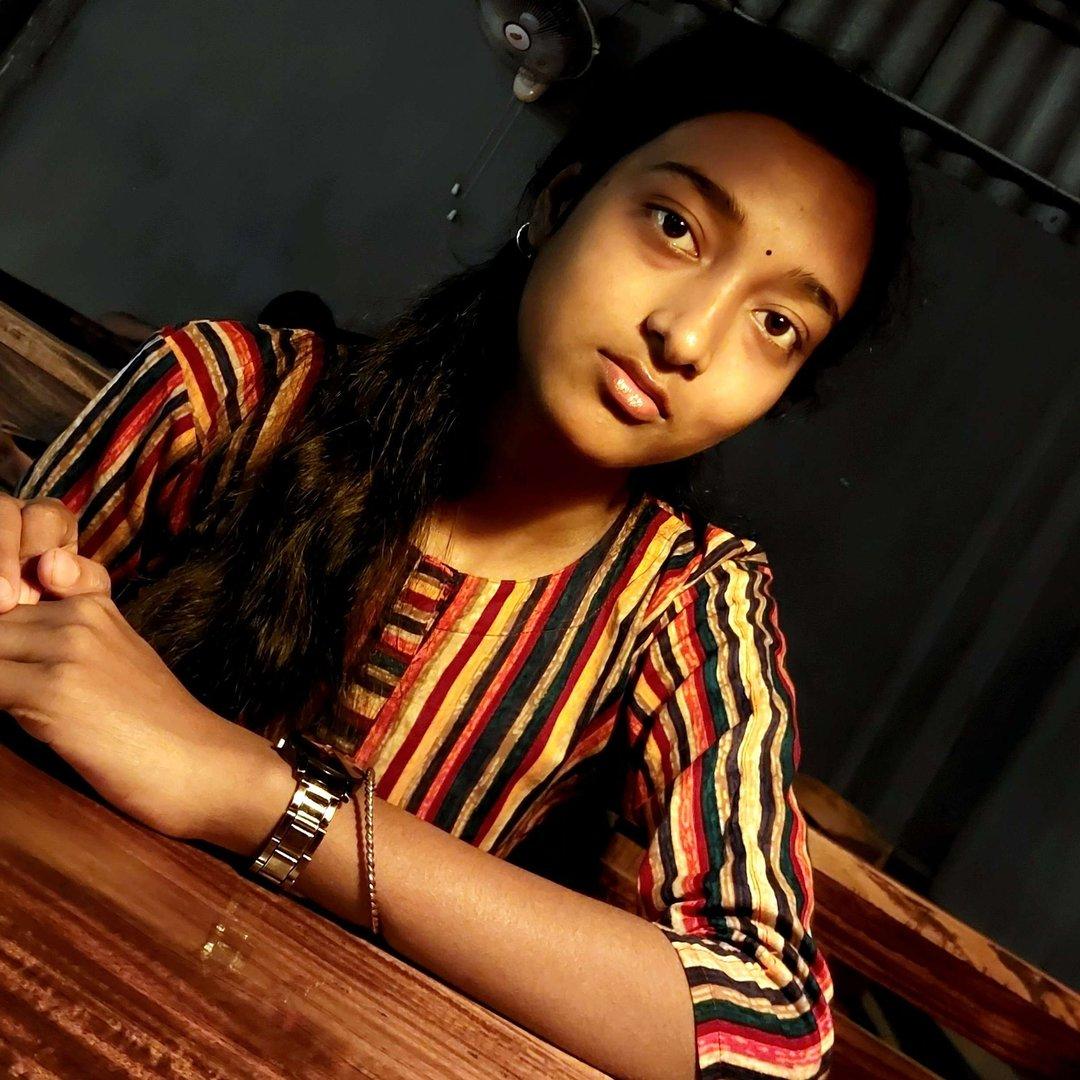
Sangita
Hi, thanks for taking a look at my profile. I'm Sangita, a blogger at Hybrowlabs, a web and mobile development firm. With a passion for storytelling, I create engaging content on technology, marketing, and lifestyle. My versatile writing style blends creativity with professionalism while staying up-to-date with industry trends. I aim to make complex concepts accessible and inspire through my words.
No comments yet. Login to start a new discussion Start a new discussion